

However, different theories have been applied to interpret the increased toughness in different cases with a variety of polymer matrices and rubber particles involved. The major theories attribute toughening mechanisms to the multiple-crazing, shear yielding, and rubber cavitation, depending on the properties of the matrix in which rubber particles are dispersed. The principles of increasing the impact strength of HPP by including elastomer/rubbers have been studied for many years and several mechanisms were proposed. Moderate impact strength improvement of HPP can also be obtained when SBS and butyl rubber are used. The most effective impact strength enhancement can be achieved through embedding EPR or EPDM particles in the HPP matrix in a specific loading level range determined by final applications.

The effect on impact properties of HPP differs with different elastomer/rubbers. The most used categories of elastomers/rubbers include ethylene-propylene rubbers (EPR), butyl rubber, styrene-butadiene-styrene (SBS) copolymer, and ethylene-propylene-diene (EPDM) copolymer. The most common way in the industry is to include elastomers/rubbers in homopolymer PP to enhance the impact strength, generating various grades of impact copolymer PP (ICPP) which have been commercialized successfully and dominate a large portion of the PP market. Blending HPP with a variety of particles, including rigid and rubber forms, has been demonstrated as an effective, simple, and economic way to optimize the material properties such as impact strength. The brittleness of HPP can be modified using different strategies. The applications of commercial homopolymer PP (HPP) are limited by its relatively low impact strength and high brittleness temperature. The importance of different requirements on the mechanical properties of PP can be demonstrated by a variety of commercial grades of PP offered by many suppliers on the market. Polypropylene (PP) possessing desired mechanical properties, especially a required impact strength at a specific temperature, is critical for many applications in different industrial sectors, including packaging, construction, and automotive.
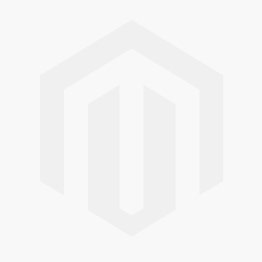
The thermal compounding process and the original material properties mainly determine the final mixture behaviors, and the mixture properties can be predicted based on the weight ratios of the two components. The crystallization peak temperatures increased linearly with increasing ICPP contents while the degrees of crystallinity of the mixtures decreased linearly. Notched and unnotched impact strengths increased linearly with increasing ICPP contents.
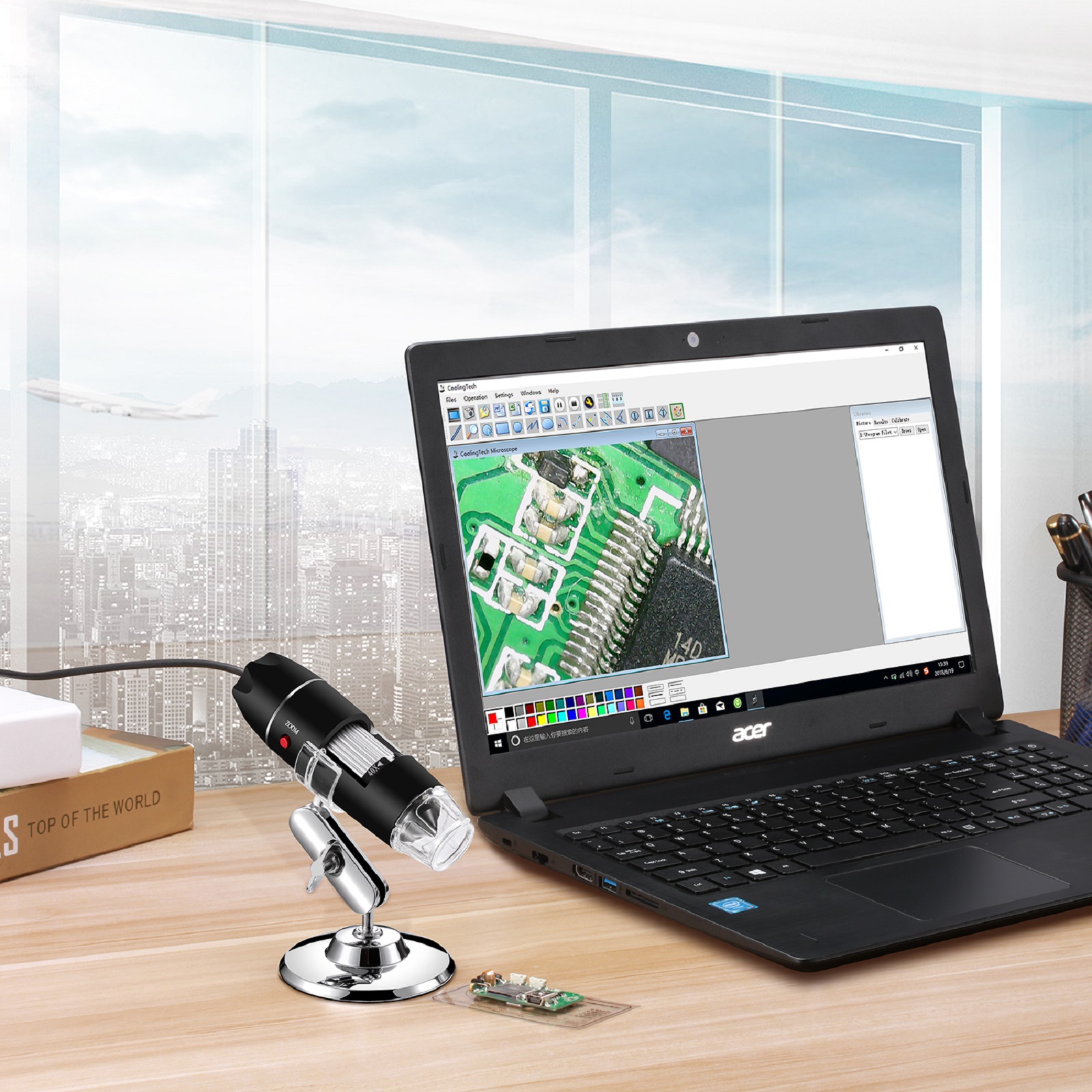
The fracture surface results indicated that the morphologies of the rubber particles in ICPP changed after compounding with HPP, leading to different mechanical and thermal behaviors of the mixtures. The mechanical behaviors, fracture surfaces, and thermal properties of the mixtures were then characterized. ICPP and HPP were compounded with an internal mixer at different ratios and then the mixtures were injection molded into specimens for characterization. This research was to provide insights for managing material supplies through formulating PP with specific mechanical properties using melt compounding of ICPP and HPP. Management of this wide range of materials is a challenge for material suppliers and manufacturers and product developers. Many grades of homopolymer polypropylene (HPP) and impact copolymer PP (ICPP) with a wide range of mechanical properties have been developed for a variety of applications in different industrial sectors.
